The Unstressed Advantage
Innovative Air Management is the sole provider of this revolutionary ePTFE technology, setting a new standard in industrial air filtration for filter manufacturers.
STRESSED
Although this process has been used for decades, it has not been without limitations. This stretching process traumatizes the fibers so that, once formed into a thin membrane, they become more fragile. This creates a stressed membrane. Pleating a stressed ePTFE membrane can create ruptures and breakage in the fibers, thus reducing efficiency and increasing resistance along every pleat line. This can lead to delamination over time.
ePTFE HISTORY
ePTFE was developed in 1938 as a frictionless material and was used during World War II in the development of the atomic bomb. Since then, PTFE has been used in a vast number of applications, including air filtration. Traditionally, PTFE fabrication for air filtration requires that the fibers be expanded by quickly stretching them to create fibers with submicronic openings. These openings allow the oxygen to pass but block the hydrogen in the water molecule (H2O).
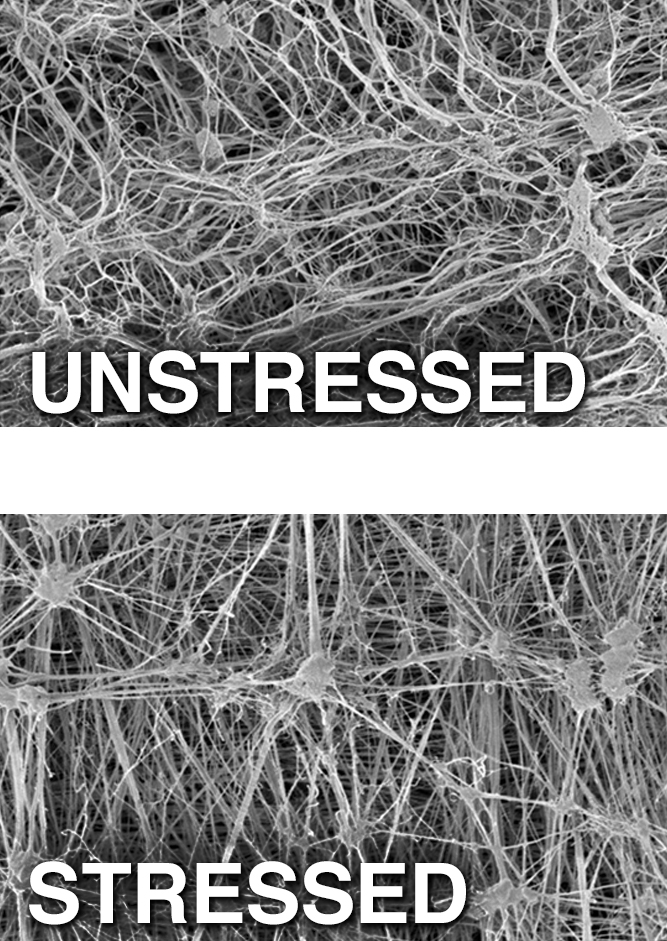